Портфельная компания РОСНАНО «Плакарт» защитила от коррозии конструкции крупнейшего небоскреба в Европе Лахта-Центра
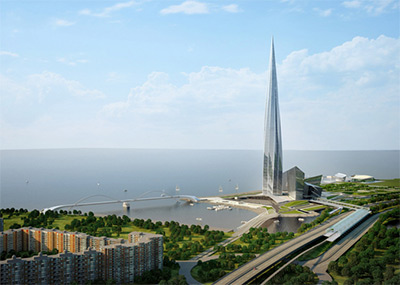
Специалисты ЗАО «Плакарт» (портфельная компания РОСНАНО) защитили от коррозии в агрессивных условиях эксплуатации основные стальные рельсы системы очистки фасада (СОФ) ультрасовременного Лахта-Центра в Санкт-Петербурге. Традиционные методы антикоррозионной защиты в данном случае были неприменимы, пишет rusnano.com.
Лахта-Центр строится в Приморском районе Санкт-Петербурга, на берегу Финского залива. Строительство будет завершено в 2018 году. Доминанта комплекса – 462-метровыйнебоскреб – станет самым высоким зданием Европы. Архитектурная и инженерная сложность сооружения диктует необходимость применения новейших технологий, поскольку традиционные технологии не позволяют решать поставленные задачи.
В частности, специально для высотного здания Лахта-Центра разработана уникальная система грузоподъемных механизмов для обслуживания (очистки и текущего ремонта) остекленных фасадов (СОФ), которая будет успешно работать на здании, имеющем скручивающуюся и выпуклую форму. Стеклянный фасад из 16 505 фрагментов разной формы. Его общая площадь составит 72 500 кв. м. Геометрия небоскреба изменяется по всей 462-метровой высоте. Здание расширяется, сужается и закручивается. 71% элементов из стекла и стали различаются по форме и размерам. Общая площадь фасадов – более 130 000 кв. м стекла, которое нужно содержать в чистоте и при необходимости ремонтировать элементы конструкций. СОФ, состоящая из кареток подъема-спуска, платформы, из направляющих рельс вдоль ребер здания, работает до высотной отметки 369 метров.
Основные стальные рельсы СОФ, находясь в агрессивных условиях эксплуатации (резкие перепады температур, морской ветер, механическое воздействие движения кареток, вибрация) подвергаются сильному воздействию коррозии. Нарушение целостности стальных конструкций ведет в итоге к сокращению эксплуатационных сроков. Основное следствие коррозии – возрастает риск опасности, и в том числе летального исхода для людей, работающих на СОФ, по причине возможного обрушения платформ.
Традиционный метод антикоррозионной защиты лакокрасочными материалами в данном случае не обеспечит долговечную надежную защиту от коррозии из-за воздействия агрессивных сред, невозможности постоянного обслуживания и контроля коррозии поверхности рельс, механическое движение кареток по рельсу нарушит целостность лакокрасочного покрытия и потребует обновления через 3-5 лет. Габариты самих деталей являются ограничением по применению метода горячего цинкования.
Специалистами «Плакарт» с учетом всех факторов было разработано и предложено решение «Напыление методом электродуговой металлизации покрытия Плакарт ТМ на основе цинка» суммарной толщиной покрытия 250 мкм. Данный способ покрытия имеет ряд преимуществ по сравнению с лакокрасочным покрытием.
- Покрытие противостоит экстремальным температурам, воздействию морской воды, ударным нагрузкам, истиранию. Лакокрасочные покрытия не обладают такими характеристиками.
- Покрытие защищает объект до 50 лет от появления следов коррозии. Обладает высокой адгезией до 80 Мпа. Основная часть (до 90%) цинка в верхних слоях покрытия, при горячем цинковании – лишь до 40%.
- Нет ограничений по габаритам и форме детали.
Электродуговая металлизация обладает следующими преимуществами:
- высокая производительность (до 40 кг/ч напыляемого металла);
- более прочные покрытия с высокой адгезией по сравнению с газопламенным способом;
- возможность использования проволок из разных металлов позволяет получить покрытие в соответствии с требованиями конкретных решений;
- невысокие эксплуатационные затраты;
- безопасность процесса.