Волгоградское стекольное предприятие увеличивает обороты производства
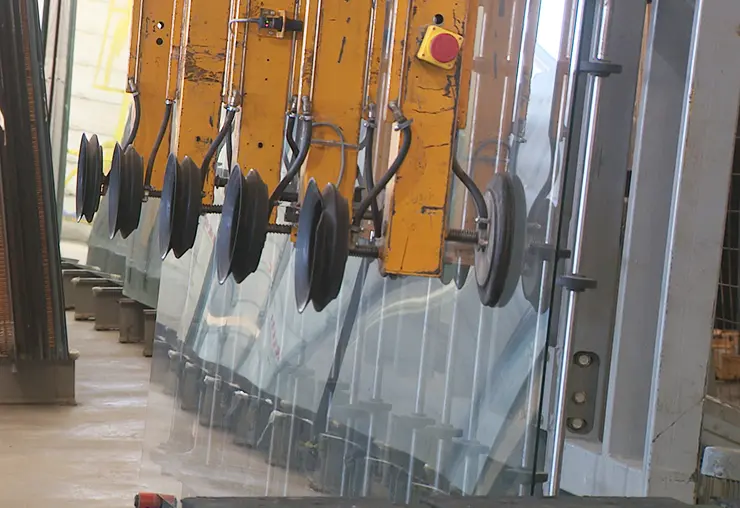
Фото: volgograd-trv.ru. Волгоградское стекольное предприятие
Санкции лишь закалили отечественные компании. И волгоградские – не исключение. Так, местное стекольное предприятие планирует увеличивать производство и изготавливать новые виды стеклопакетов. Отчасти способствует этому и приобретение волгоградских 5D-принтеров, которые изготавливают детали для зарубежного оборудования.
Футбольный стадион международного класса – «Волгоград Арена». Один из лучших в мире по мнению спортсменов и болельщиков. Здание аэропорта, которое первым встречает всех гостей города-героя и, конечно, речпорт – все эти знаковые для города объекты имеют свой уникальный внешний вид благодаря предприятию из Волгограда. Сотрудники до сих пор помнят, как изготавливали стекло для этих проектов.
«Нас всех собрали, объявили, что это ответственная задача. Нам и самим было интересно. Собственно, речпорт нам не чужой, так как это наше наследие. Был такой подъем коллективный. Ребята работали с энтузиазмом», – вспоминает начальник сервисной службы Андрей Таможников.
Начинается работа со стеклом с раскройки. Мастер по резке, как портной, размечает с помощью компьютера размеры заготовок. Само «прозрачное полотно» на стол доставляет специальный кран с присосками. В зависимости от толщины такой лист может весить до 500 килограммов.
Далее начинается обработка стекла: шлифовка краев, придание необходимой формы и отверстий. Для того, чтобы лист не перегрелся и не треснул, его охлаждают водой. Для этих целей используют различные станки в зависимости от расположения заготовок: вертикально или горизонтально.
Есть и, так называемая, «чистая комната», где постоянно работает климатическая установка, которая поддерживает температуру не выше 24 градусов – это необходимо для сохранности чернил принтера. А чистым помещение должно быть, чтобы ни одна пылинка не попала на стекло во время печати.
«Оборудование мы планируем использовать для покраски стекол, для наземного транспорта. Потом мы отправили образцы в крупнейшую компанию по изготовлению солнечных батарей, где тоже идет градиентная печать», – говорит начальник цеха архитектурного направления Владимир Гончаров.
Приобрели принтер в прошлом году. Для дизайнерских решений он открыл безграничные возможности. Так, например, вскоре здесь сделают витражи для ставропольского аэропорта с портретом Александра Суворова. Когда стекло уже прошло обработку и печать, остается финальный этап – закаливание.
В печи закаливания стекло нагревается до температуры 650-680 градусов. Таким образом, оно становится гораздо прочнее: ему ни по чем перепады температур в 200 градусов. Также механическая прочность увеличивается в 4-6 раз – один лист выдерживает вес взрослого человека.
Толщина стекла всего в четыре миллиметра. Предприятий, у которых есть такие печи закаливания, в России не так уж много. В условиях санкций купить их становится еще труднее. Непростая ситуация и с комплектующими для различного оборудования. Выход удалось найти: необходимые детали для импортных машин теперь печатают на 5D-принтере, который разработали волгоградские инженеры.
«Он позволяет печатать всевозможные детали для наших станков: как на пластике, так и на резиновые изделия. Так мы обезопасили свое производство от длительных простоев оборудования. Сейчас наши сервисные инженеры легко изготавливают нужную нам деталь», – поясняет руководитель центра продаж Геннадий Улисков.
Как говорят руководители предприятия, санкции лишь закалили компанию. Конечно, некоторые логистические цепочки пришлось перестроить, наблюдался росте цен на сырье и готовую продукцию. Зато на отечественном рынке стали появляться новые разработки.
«Наши же поставщики научились изготавливать подобные вещи уже в России. Вот вторую печь, которую мы купили, уже российской сборки. Она усовершенствована, однако эта печь, конечно, не такая высокотехнологичная, но это начало, может быть, в дальнейшем наши компании научатся делать более технологичные вещи», – говорит Геннадий Улисков.
Специалисты предприятия отмечают, прошлый год был весьма успешным. Удалось увеличить мощности в 2-2,5 раза благодаря приобретению нового оборудования. Также в начале 2022 года было запущено промышленное производство душевых кабин. Уже в планах на этот год установка второй, более современной линии сборки стеклопакетов.
«Мы увеличиваем производительность в 2-2,5 раза и начинаем изготавливать принципиально новые виды стеклопакетов, которые до этого не делали. Максимальный стеклопакет, который сможем делать, – это размером 2400 х 4800 толщиной 80 миллиметров. Оборудование рассчитано на максимальный вес стеклопакета в 1,2 тонну», – рассказывает руководитель центра продаж.
Сейчас компания входит в лидеры по производству стеклопакетов в ЮФО. В планах приобретать новое оборудование, и наращивать производственные мощности на всех восьми заводах, которые расположены в разных регионах нашей страны.
Рекомендуем прочесть: Волгоградское предприятие модернизирует производство архитектурных стеклопакетов с помощью господдержки
Текст: Сергей Вечеркин, https://volgograd-trv.ru